Speedmaster XL 106 for label printing.
The Speedmaster XL 106 automates the production of sophisticated wet-glue or in-mould labels (IML). The costs per sheet are lowered.
Set standards in wet glue or in-mould label production.

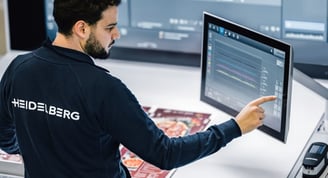
Information provider, advertising medium and basis for innovative security features: Labels are increasingly becoming brand ambassadors. The Speedmaster XL 106 is our answer to an expanding market in which the enormous variety of products leads to short print runs and packaging forms must adhere to increased environmental awareness.
At a glance


In-mould labels
Lightweight and thin materials place particular demands on statics and sheet travel. The Speedmaster XL 106 counters this with special equipment.
High performance for challenging materials
Thanks to innovative components on the feeder and delivery, including supporting preset functions and optimized sheet travel, the Speedmaster XL 106 with IML Performance Equipment 4.0 effortlessly processes materials from a thickness of 40 μm.
Optimal drying
An extended drying section in the Y-units as well as hot air and infrared settings in one percent increments of the DryStar Advanced dryer enable gentle processing of delicate materials and perfect register even with thin plastic films. Automation, preset functions and storable settings reduce set-up times.
In the DryStar Monitor, sensors for temperature, humidity and air volume, including data storage, data transfer to the PC, software program for evaluation and connection to printing machine’s wallscreen, show the actual status of the dryers. The air volume of the exhaust air, the relative humidity (RH in %) and temperature of the supply and exhaust air as well as the absolute humidity (g H2O/kg air) and the amount of extracted water in the exhaust air (kg/water/h) are displayed.
Full drying control


Wet glue labels
Thanks to its innovative components, reduced waste and production speeds of up to 21,000 sheets per hour, the Speedmaster XL 106 enables wet-glue labels to be produced economically.
Short set-up times and top speeds
Thanks to innovative components on the feeder and delivery, including supporting preset functions and optimized sheet travel, the Speedmaster XL 106 with IML Performance Equipment 4.0 effortlessly processes materials from a thickness of 40 μm.
Simulation of spot colors
The Prinect Multicolor Toolset spot color simulation using the four process colors as well as orange, green and violet reproduces a large color space and avoids color changes and wash times. This makes it possible to display different spot colors on one sheet. Using Print Color Management, the Multicolor workflow provides a standardized printing process with stable, reproducible quality.
Sustainable label production
The energy-efficient dryer DryStar Combination Eco saves up to 30 percent energy thanks to optimized energy input, integrated heat recovery and thermal insulation. The high level of insulation reduces energy consumption during drying and minimizes heat loss. The pressroom heats up less. Less air conditioning is required. The workplace becomes more user-friendly.
At a glance




Lightweight and thin materials place particular demands on statics and sheet travel. The Speedmaster XL 106 counters this with special equipment.
In-mould labels
Wet glue labels
Thanks to its innovative components, reduced waste and production speeds of up to 21,000 sheets per hour, the Speedmaster XL 106 enables wet-glue labels to be produced economically.
High performance for challenging materials
Optimal drying
Full drying control
Thanks to innovative components on the feeder and delivery, including supporting preset functions and optimized sheet travel, the Speedmaster XL 106 with IML Performance Equipment 4.0 effortlessly processes materials from a thickness of 40 μm.
An extended drying section in the Y-units as well as hot air and infrared settings in one percent increments of the DryStar Advanced dryer enable gentle processing of delicate materials and perfect register even with thin plastic films. Automation, preset functions and storable settings reduce set-up times.
In the DryStar Monitor, sensors for temperature, humidity and air volume, including data storage, data transfer to the PC, software program for evaluation and connection to printing machine’s wallscreen, show the actual status of the dryers. The air volume of the exhaust air, the relative humidity (RH in %) and temperature of the supply and exhaust air as well as the absolute humidity (g H2O/kg air) and the amount of extracted water in the exhaust air (kg/water/h) are displayed.
Sustainable label production
Thanks to innovative components on the feeder and delivery, including supporting preset functions and optimized sheet travel, the Speedmaster XL 106 with IML Performance Equipment 4.0 effortlessly processes materials from a thickness of 40 μm.
Simulation of spot colors
Short set-up times and top speeds
The Prinect Multicolor Toolset spot color simulation using the four process colors as well as orange, green and violet reproduces a large color space and avoids color changes and wash times. This makes it possible to display different spot colors on one sheet. Using Print Color Management, the Multicolor workflow provides a standardized printing process with stable, reproducible quality.
The energy-efficient dryer DryStar Combination Eco saves up to 30 percent energy thanks to optimized energy input, integrated heat recovery and thermal insulation. The high level of insulation reduces energy consumption during drying and minimizes heat loss. The pressroom heats up less. Less air conditioning is required. The workplace becomes more user-friendly.
The Speedmaster XL 106 automates the production of sophisticated wet-glue or in-mould labels (IML). The costs per sheet are lowered.
Technical data
Q
Printing stock
Max. sheet size
750 mm x 1,060 mm (29.53 in x 41.73 in)
340x480 mm (13.39x18.90 in) straight printing
410x480 mm (16.14x18.90 in) in perfecting mode/straight printing/18,000 sph
440×600 mm (17.3×23.62 in) with Auto-Nonstop operation delivery
Min. sheet size
Max. print format
740 mm x 1,050 mm (29.13 in x 41.34 in) straight printing
730 mm x 1,050 mm (28.74 in x 41.34 in) perfecting mode
0.03–1.00 mm (0.0012×0.039 in) w/o perfecting device, w/o Auto-Nonstop operation delivery
0.03–0.80 mm (0.0012×0.031 in) with perfecting device, w/o Auto-Nonstop operation delivery
Thickness
Thickness with auto-nonstop
0.07–1.00 mm (0.0028×0.039 in) w/o perfecting device, with Auto-Nonstop operation delivery
0.07–0.80 mm (0.0028×0.031 in) with perfecting device and Auto-Nonstop operation delivery
10 mm – 12 mm (0.39 in – 0.47 in) thickness < 0.8 mm (0.03 in)
11 mm – 12 mm (0.43 in – 0.47 in) thickness > 0.8 mm (0.03 in)
Gripper margin
Q
Print output
Min. sheet size
18,000 sph (standard straight printing presses)
15,000 sph (standard perfecting presses)
18,000 sph (option perfecting presses)
21,000 sph (option)
Q
Plates
Length x width
Thickness
811 mm × 1,055 mm (32.24 in × 41.54 in)
0.24 mm - 0.30 mm (0.009 in - 0.012 in)
Q
Coating blanket cylinder
Length x width, coating blanket
Length x width, coating plate
Max. coating area
Cylinder undercut
Distance from lead edge of coating plate to lead edge of coating
828 mm x 1,072 mm (32.60 in x 42.20 in) metal-barred
819 mm x 1,060 mm (32.24 in x 41.73 in)
740 mm x 1,050 mm (29.13 in x 41.34 in)
3.20 mm (0.126 in)
43 mm (1.69 in)
Q
Coating blanket cylinder
Basis
Speedmaster XL 106-6+L with two delivery extension modules.
Number of printing units
6
1
Number of coating units
Length
Width
Height
16.50 m (649.61 in)
3.93 m (154.72 in)
2.33 m (91.73 in)
Q
Plate cylinder
Cylinder undercut
Distance from lead edge of plate to lead edge of print
0.10 mm (0.004 in)
53 mm (2.09 in)
Q
Blanket cylinder
885 mm x 1,077 mm (34.84 in x 42.40 in) metal-barred
Length x width, blanket
Thickness blanket
Length x width, packing sheet
Cylinder undercut
1.95 mm (0.077 in)
765 mm × 1,052 mm (30.12 in × 41.42 in)
2.30 mm (0.091 in)
Q
Pile heights
Feeder
1,320 mm (51.97 in) incl. pile table and pile support plate / elevated +525 mm (20.67 in) or +875 mm (34.45 in)
Delivery
1,295 mm (50.98 in) incl. pile table and pile support plate / elevated +525 mm (20.67 in) or +875 mm (34.45 in)
Technical data can vary according to job, consumables, printing stock and, possible, other factors.
Powered by Prinect
Prinect Production digitizes your print shop. It automates production and color and quality management while also providing key data for analyses and reporting. You retain your customers and maximize your performance with a smart workflow.
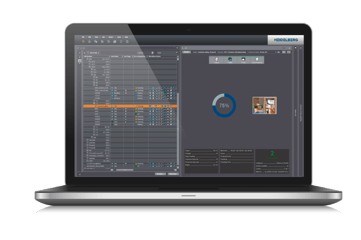
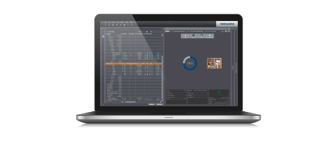
Trusted HEIDELBERG Dealer
Innovative printing solutions for your business needs.
Excellence
Precision
info@heidelberg.hr
info@heidleberg.si
info@heidelberg.rs
© 2024. All rights reserved.