Versatile and compact
platesetters.
Suprasetter A75.
Whilst the basic manual feed CtP has a very small footprint, a Suprasetter A75 with auto plate loading system is by far the smallest platesetter in its class – the ideal pre-condition for being able to invest in Computer-to-Plate (CtP) production without having to restructure.
Fully equipped with the technology of a high-end machine
The Suprasetter A75, which is fully equipped with the technology of a high-end machine, offers outstanding performance features.
Low consumption for the benefit of the environment: The Suprasetter A75 has the lowest energy usage in its class and it has the lowest heat output. This also has a positive effect on the energy balance. There is no need for additional air-conditioning at up to 30 degree Celsius (86 degree Fahrenheit) ambient temperature. The minimal electricity requirement provides substantial long term, cost savings along with being environmentally friendly.
Can be configured for various thermal plates: The Suprasetter A75 offers the right configuration for every type of plates. For example, an online processor can be connected for conventional thermal plates, a clean out unit for chemical-free thermal plates as well as a plate stacker for process-free thermal plates.
At a glance
The most space-saving and successful CtP Platesetter in its class
Configurable for conventional, processless and chemical-free thermal plates
Low in energy consumption – high in eco-friendliness
Operational within a day
Key features
Laser technology by HEIDELBERG
A Suprasetter A75 uses the same proven laser technology as all the other models in the Suprasetter series. Production reliability is ensured through the Intteligent Diode System (IDS). This means that if a diode fails, operation can continue. The laser systems developed exclusively by HEIDELBERG deliver reliable imaging quality.
Compact full automation for small and medium formats
With the option Dual Top Loader (DTL), a manual Suprasetter A75 provides fully automated plate loading with slip sheet removal. This loader module can be easily installed on the basic unit. Due to an additionally integrated tray, the Dual Top Loader (DTL) offers two different plate formats (2-up and 4-up) in parallel for completely automatic changing. The investment in a DTL pays off in no time due to mostly unattended operation.
Highest punching accuracy
Suprasetter can be optionally equipped with highly accurate internal punching systems. The punched plates provide maximum register accuracy. This reduces press makeready times which also minimizes waste.
Debris Removal System
The Debris Removal System is an optional vacuum and filtration system that removes loose particles and dust. When fitted with this option, the Suprasetter A75 is also fully equipped to process ablative plates.
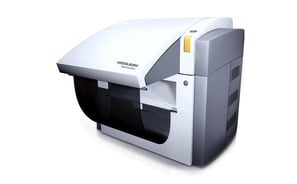
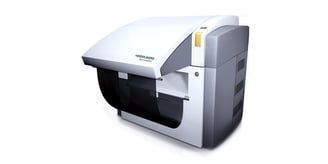
Technical data
Throughput option
(plates/h in max. format)Auto Pallet Loader
(APL)Auto Cassette Loader (ACL)
Dual Cassette Loader (DCL)
Dual Top Loader
(DTL)
Number of cassettes
Cassette capacityDimensions
(width × depth × height)Min. plate format
(height × width)Max. plate format
(height × width)Max. imaging format
(height × width)Plate thickness
Resolution
17/22
/
/
/
yes
max. 2 cassettes
up to 50 plates 0.3 mm
up to 100 plates 0.15 mm1.550 × 1.218 × 1.350 mm
240 × 240 mm
676 × 760 mm
656 × 760 mm
0,15–0,3 mm
2.400 dpi or 2.540 dpi
Optional 5.080 dpi
Register accuracy
Internal punches
Operating temperature
Relative humidity
Ambient conditions
Suction and dust filter system
Temperature stabilizer
Intelligent Diode System (IDS)
Smart Plate Handling
Suprasetter Lenticular Resolution Adjustment
Workflow integration
Power consumption
± 25 μm with four consecutive exposures
using the internal punching system
± 5 μm with two consecutive exposures
on the same plateup to 2 pairs of punches
17 °–30 °C
30–70 %
/
Option
/
Standard
Standard
/
Prinect Prepress Manager, Prinect MetaDimension, Prinect Shooter
< 700 W average, 550 W power
consumption during exposure
Technical data can vary according to job, consumables, printing stock and, possible, other factors.
Trusted HEIDELBERG Dealer
Innovative printing solutions for your business needs.
Excellence
Precision
info@heidelberg.hr
info@heidleberg.si
info@heidelberg.rs
© 2024. All rights reserved.